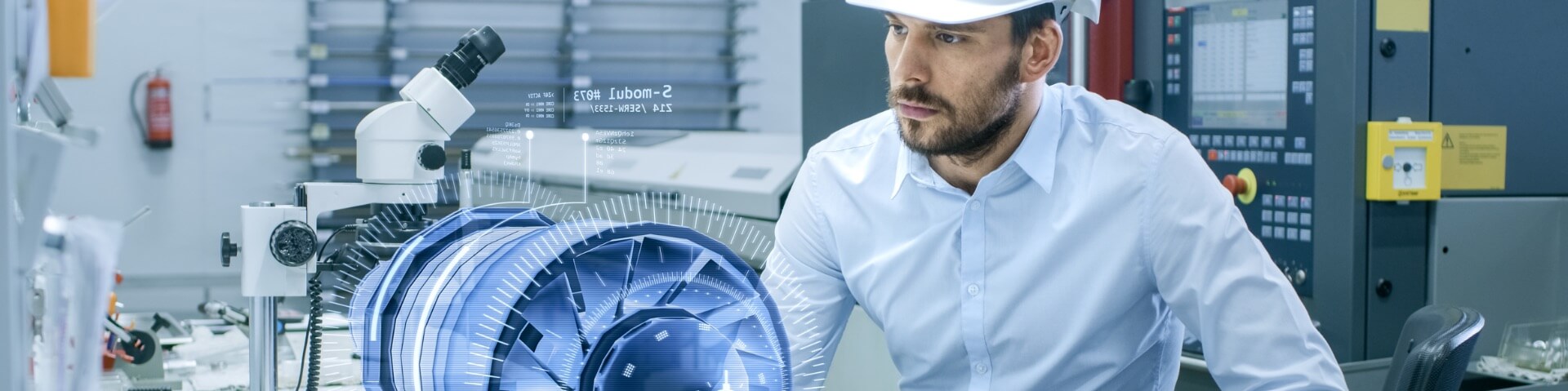
Selective Laser Sintering (SLS) 3D Printing Services
Rapid PSI leverages advanced Selective Laser Sintering (SLS) services to bring your manufacturing ideas to life. Serving clients across Wichita, KS, we are the premier local destination for advanced SLS technology for customized parts.
Whether you are a manufacturer or engineer needing high-quality 3D printing services, count on us to have the expertise and equipment to meet your prototyping and production needs. Experience the Rapid PSI difference in custom SLS parts
Understand Selective Laser Sintering (SLS) Services
Selective Laser Sintering (SLS) is a revolutionary additive manufacturing technique. It utilizes a high-powered laser to sinter powdered materials layer by layer. This process creates complex and durable 3D-printed objects with exceptional precision and detail. At Rapid PSI, we harness the power of SLS technology to provide you with exceptional results that surpass traditional manufacturing methods.
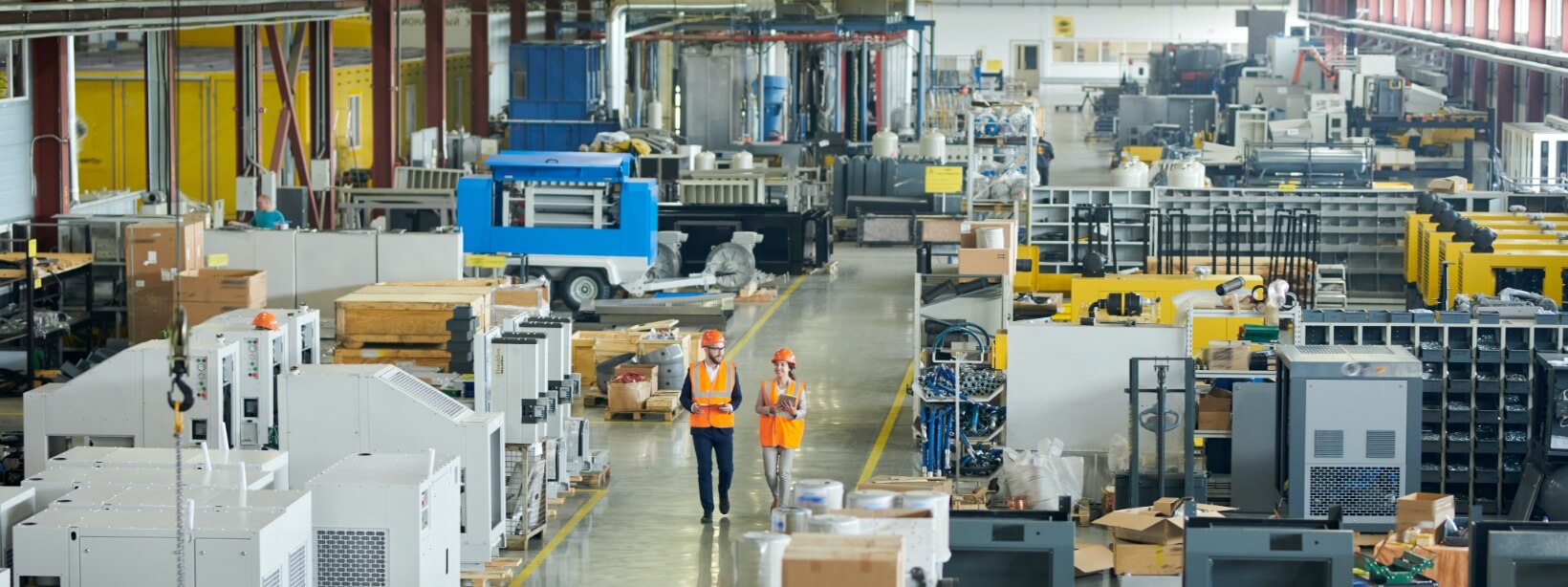
Experience the Advantages of SLS 3D Printing
SLS printing offers numerous advantages, making it an ideal choice for various applications. The key benefits of our SLS 3D printing services include the following:
- Design freedom: Bring your most intricate designs to life. The layer-by-layer construction process surpasses conventional manufacturing techniques by making it possible to produce complex geometries, internal cavities, and organic shapes.
- Versatility: Our SLS printers build parts with Nylon 12 PA at various layer thicknesses.. This versatility opens up endless possibilities for creating functional prototypes, end-use parts, and customized products tailored to your specific requirements.
- Speed and efficiency: SLS printing has rapid production capabilities. By eliminating the need for tooling or molds, we significantly reduce lead times, allowing you to accelerate your product development cycle. Bring your innovations to market faster with our 3D printing solutions.
- Exceptional quality: Our SLS printing services deliver superior accuracy and surface finish. We ensure that we faithfully replicate every detail of your design. The durability and strength of SLS-produced parts make them suitable for demanding applications in various industries.
Why Us: Discover the Rapid PSI Difference
Rapid PSI is the go-to SLS 3D printing services provider in Wichita, KS, and beyond. Choose us for our:
- Cutting-edge technology: We stay at the forefront of SLS technology to provide you with the best possible results. Our state-of-the-art 3D printers and equipment guarantee exceptional print quality and reliability.
- Expertise and experience: Since 1998, our team of skilled engineers and technicians has been mastering SLS printing and producing high-quality results. We understand the intricacies of the process and can guide you through every step of the manufacturing journey.
Custom solutions: We take a personalized approach to each project and tailor our services to meet your unique requirements and ensure success. Whether you need a one-off prototype or a large-scale production run, we can help.
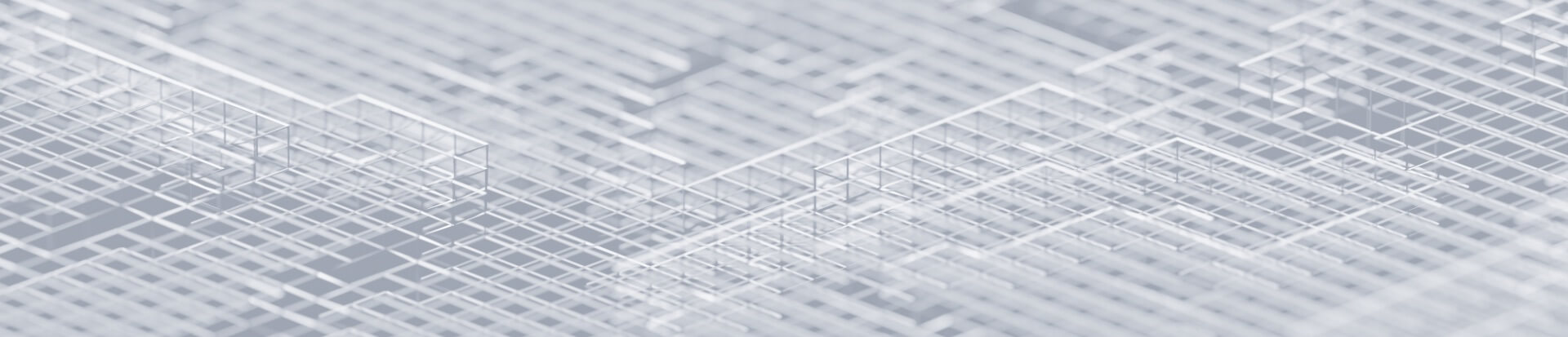
Get Started
Rapid PSI is standing by to discuss your 3D printing needs. We are eager to help you understand our rapid prototyping services and how we can bring your ideas to life. With the power of 3D printing in our grasp, we can help you unlock new possibilities for your business or project. Let Rapid PSI be your trusted partner in the world of rapid prototyping.